It’s a bit like a Marvel superhero comic or a 70s sci-fi TV show—only it actually just happened. After having his sternum and several ribs surgically removed, a Spanish cancer patient took delivery of one titanium 3D printed rib cage—strong, light, and custom fit to his body.
It’s just the latest example of how 3D printing and medicine are a perfect fit.
The list of 3D printed body parts now includes dental, ankle, spinal, trachea, and even skull implants (among others). Because each body is unique, customization is critical. Medical imaging, digital modeling, and 3D printers allow doctors to fit prosthetics and implants to each person’s anatomy as snugly and comfortably as a well tailored suit.
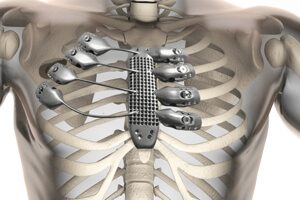
In this case, the 54-year-old patient suffered from chest wall sarcoma, a cancer of the rib cage. His doctors determined they would need to remove his sternum and part of several ribs and replace them with a prosthetic sternum and rib cage.
Titanium chest implants aren’t new, but the complicated geometry of the bone structure makes it difficult to build them. To date, the typically used flat plate implants tend to come loose and raise the risk of complications down the road.
Now, we can do better. We have the technology.
Complexity is free with 3D printing. It’s as easy to print a simple shape as it is to print one with intricate geometry. And with a 3D model based on medical scans, it’s possible to make prosthetics and implants that closely fit a patient’s body.
But it takes more than your average desktop Makerbot to print with titanium.

The surgeons enlisted Australian firm Anatomics—the company that designed a 3D printed skull implant to replace nearly all of a patient’s cranium last year—and CSIRO’s cutting-edge 3D printing workshop, Lab 22, to design and manufacture the implant.
Lab 22 owns and operates a million-dollar Arcam printer. Most 3D printed metal parts use a technology called selective laser sintering, in which layers of powdered metal are fused with a laser beam. Instead of a laser, however, the Arcam printer uses a significantly more powerful electron beam technology developed for aerospace applications. (GE, for example, is printing titanium aluminide turbine blades with the tech.)
The surgeons worked closely with Anatomics to design the implant based on CT scans of the patient’s chest. Using a precise 3D model, the printer built the titanium implant—a sternum and eight rib segments—layer by layer. The final product is firmly attached to the patient’s remaining rib cage with screws.
According to CSIRO’s Alex Kingsbury, “It would be an incredibly complex piece to manufacture traditionally, and in fact, almost impossible.”
Once complete, the team flew the implant to Spain for the procedure. All went to plan. The patient left hospital 12 days after the surgery and is recovering well.
While customization is widely used to illustrate 3D printing’s power, it can often be more of a perk than a necessity. In many cases, traditional mass manufacturing methods still make more sense because they’re cheaper and faster.
In some industries, however, customization is critical.
Aerospace firms, for example, are making 3D printed parts for jet and rocket engines—where rapid prototyping speeds up the design process, and cheap complexity and customization yields parts that can’t be made any other way.
And nowhere is customization more useful than in medicine. From affordable custom prosthetics to tailor-made medical implants to bioprinted organs—the potential, in terms of improving and even saving lives, is huge.
We can’t rebuild and replace every body part yet, but that’s where we’re headed.