The 3D printing (digital manufacturing) market has had a lot of hype over the past few years.
Most recently, it seems this technology arena has entered the “trough of disillusionment,” as 3D printing stock prices have taken a hit. But the fact remains: this exponential technology is still in its childhood and its potential for massive disruption (of manufacturing and supply chains) lies before us.
This article is about 3D printing’s vast potential — our ability to soon 3D print complex systems like jet engines, rocket engines, cars and even houses.
But first, a few facts:
- Today, we can 3D print in some 300 different materials, ranging from titanium to chocolate.
- We can 3D print in full color.
- We can 3D print in mixed materials — imagine a single print that combines metals, plastics and rubbers.
- Best of all, complexity and personalization come for free.
What Does It Mean for “Complexity to Be Free”?
Think about this: If you 3D print a solid block of titanium, or an equal-sized block with a thousand moving components inside, the time and cost of both 3D printings is almost exactly the same (the solid block is actually more expensive from a materials cost).
Complexity and personalization in the 3D printing process come for free — i.e. no additional cost and no additional time. Today, we’re finding we can 3D print things that you can’t manufacture any other way.
Let’s take a look at some of the exciting things being 3D printed now.
3D Printing Rocket Engines

In 2014, SpaceX launched its Falcon 9 rocket with a 3D-printed Main Oxidizer Valve (MOV) body in one of the nine Merlin 1D engines (the print took less than two days —whereas a traditional castings process can take months).
Even more impressive, SpaceX is now 3D printing its SuperDraco engine chamber for the Dragon 2 capsule.
According to SpaceX, the process “resulted in an order of magnitude reduction in lead-time compared with traditional machining — the path from the initial concept to the first hotfire was just over three months.”
On a similar note, Planetary Resources Inc. (PRI) is demonstrating the 3D printing of integrated propulsion and structures of its ARKYD series of spacecraft. This technology has the potential to reduce the parts count by 100x, with an equal reduction in cost and labor.
3D Printing Jet Engines
GE has just demonstrated the 3D printing of a complete, functioning jet engine (the size of a football), able to achieve 33,000 RPM.

3D printing has been used for decades to prototype parts — but now, with advances in laser technology, modeling and printing technology, GE has actually 3D printed a complete product.
Xinhua Wu, a lead researcher at Australia’s Monash University, recently explained the allure of 3D printed jet engines. Because of their complexity, she noted, manufacturing jet engine parts requires on the order of 6 to 24 months. But 3D printing reduces manufacturing time to something more like one to two weeks.
“Simple or complex, 3D printing doesn’t care,” she said. “It produces [parts] in the same time.”
3D Printing Cars
Last year, Jay Rogers from Local Motors built a 3D printed car.

It’s made of ABS plastic reinforced with carbon fiber. As they describe, “Everything on the car that could be integrated into a single material piece has been printed. This includes the chassis/frame, exterior body, and some interior features. The mechanical components of the vehicle, like battery, motors, wiring, and suspension, are sourced from Renault’s Twizy, an electric powered city car.”
It is called “The Strati,” costs $15,000, and gets 80 kilometers range on a single charge. Today, the car takes 44 hours to print, but soon the team at Local Motors plans to cut the print process to less than 24 hours.
In the past, producing a new car with a new design was very expensive and time consuming — especially when it comes to actually designing the tooling to handle the production of the newly designed car.
With additive manufacturing, once you’ve designed the vehicle on a computer, you literally press *print*.
3D Printing Houses
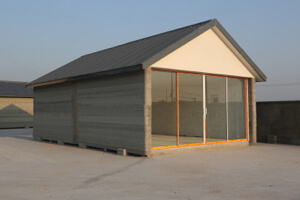
In China, a company called WinSun Decoration Design Engineering 3D printed 10 full-sized houses in a single day last year. They used a quick-drying concrete mixture composed mostly of recycled construction and waste material and pulled it off at a cost of less than $5,000 per house. Instead of using, say, bricks and mortar, the system extrudes a mix of high-grade cement and glass fiber material and prints it, layer by layer.
The printers are 105 feet by 33 feet each and can print almost any digital design that the clients request. The process is environmentally friendly, fast and nearly labor-free.
Manufacturing Is a $10 Trillion Business Ripe for Disruption
We will continue to see advances in additive manufacturing dramatically changing how we produce the core infrastructure and machines that makes modern life possible.
Image Credit: Local Motors, SpaceX, GE, WinSun