NASA recently announced that they test fired a research rocket engine. Nothing special about that—other than the fact said engine was 75 percent 3D printed parts.
As industrial 3D printing has moved from prototyping to actually manufacturing finished products, the aerospace industry has become an avid early adopter. Although in many industries mass production techniques still make economic sense—for the ultra-precise, almost bespoke parts in rockets? 3D printing is a great fit.
Last year, GE showed off a scaled down 3D printed jet engine firing at 33,000 RPM. SpaceX’s recent recovery of a Falcon 9 rocket was not only spectacular, but the rocket has long used 3D printed parts too. And NASA’s latest trial shows 3D printing is set to become an even bigger part of rocket engine manufacturing.
The NASA test used a “breadboard engine” where the parts are spread out to accommodate sensors and instrumentation for measuring each 3D printed part’s performance. But despite this research configuration, the parts themselves simultaneously experienced the same heat and stress of a normal rocket firing.
“The turbopump got its ‘heartbeat’ racing at more than 90,000 revolutions per minute (rpm) and the end result is the flame you see coming out of the thrust chamber to produce over 20,000 pounds of thrust,” said NASA’s Nick Case. “An engine like this could produce enough power for an upper stage of a rocket or a Mars lander.”
3D printing is well suited to aerospace applications for more than just the fact it can be easily customized. 3D printed components typically have fewer parts in need of joining and assembling. The turbopump in NASA’s recent engine test, for example, had 45% fewer parts than a traditional design.
3D printing also speeds up research and development. Engineers can design a part, print it, test it, find flaws, fix them, and repeat. It takes less time to get from initial design to final part than using traditional casting and the quality is often better.
All that saved time not only accelerates progress but also reduces cost.
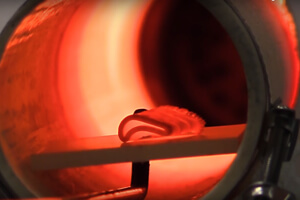
To date, 3D printed rocket parts have been made of advanced metals (e.g., SpaceX uses a superalloy called Inconel). But adding new materials should make the technology even more useful. Ceramics, for example, are another key aerospace ingredient.
Ceramics are tough materials with a high melting point. They’ve been used as heat shielding on the outside of spacecraft—think the ceramic tiles on the underside of the Space Shuttle that protected it on reentry—and as components in the fiery insides of engines and rocket nozzles.
Until recently 3D printed ceramics were poor quality compared to traditional ceramics. But new research suggests 3D printed ceramics may be on the way.
HRL Laboratories, owned by General Motors and Boeing, is developing a technique using stereolithography—a process where a liquid, or in this case a pre-ceramic resin, is selectively hardened by a laser—to build 3D structures. After firing in a kiln, the end product is much stronger than existing 3D printed ceramics and can resist temperatures of 1700°C.
The researchers think 3D printed ceramics may be used in jet engines or to skin entire jets to withstand the high temperatures of hypersonic flight. For much the same reasons, they could prove useful in rockets and spacecraft too.
These are just two examples of how 3D printing processes and techniques are helping to make better rockets faster and cheaper. It isn’t the only technology at play, but it seems poised to become increasingly important in the future.
And although it’s still mostly speculative, 3D printing’s real value to space exploration may only become clear once we leave Earth.
Lacking the luxury of sprawling factory assembly lines in space, 3D printers designed specially for space travel may be one of the pillars of off-Earth manufacturing. Some dream of mining raw materials on asteroids, moons, or planets and converting them into useful things like habitats, machines, and tools. For future explorers to be self-sufficient on the final frontier, they’ll need to live off the land.
But all that is still years away.
For now, the focus is on building better ships to more reliably leave Earth, and 3D printing looks to be a key new tool in that process.
Image Credit: NASA/MSFC; HRL Laboratories/YouTube