Historically, the only way to get anything into orbit has been by rocket; a process that is massively expensive, cumbersome, and presents a slew of constraints.
So, when Made In Space created the first zero-gravity 3D printer, it was understandably a big deal. For the first time, astronauts wouldn’t have to wait for the next launch from Earth for everything they needed—instead, they could take electronic delivery of a computer file and make tools, like this 3D printed ratchet.
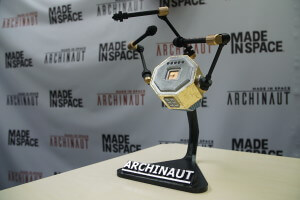
The company plans to send up a full-time, working successor to their prototype this year, but their small-scale printer is a stepping-stone to something bigger—Archinaut, the company’s new project to build large-scale structures in space.
Awarded this past November through NASA’s Tipping Point Technologies Solicitation, Archinaut is a private-public partnership funded by a two-year $20 million contract from NASA. Made In Space is partnering with Northrop Grumman and Oceaneering Space Systems to build a combination 3D printer and robotic arm that will operate in orbit outside the International Space Station.
Simply? It’s a robot that lives in space.
The robot’s body is a 3D printer that makes parts from a digital design, which can be even larger than the printer itself. A robotic arm attached to the printer can piece these homegrown parts together with other pre-fabricated parts into a larger structure. No human required.
The initial phase of the project will wrap up in 2018 when Archinaut will demonstrate the ability to 3D print and assemble structures in orbit. If all goes to plan, the team hopes to scale the printer up and add more robotic arms.
And that’s when the fun begins. The in-orbit manufacturing Archinaut promises would liberate missions from the typical constraints of launch.
Currently, structures destined for orbit need to withstand Earth gravity, be folded up as cargo, endure the rigors of launch, and survive space’s harsh environment. With Archinaut, engineers could design and build for space—and only space. Instead of sending up complete structures, we might launch key components such as sensors, electronics, and batteries along with raw materials to print the big stuff.
If we’re settling the final frontier, Rush says, “SpaceX is building the covered wagon, we’re building the pickaxes, and Archinaut is one of those tools.”
The implications are huge. Large orbital structures may include spacecraft, satellites, or other research and telecommunications infrastructure.
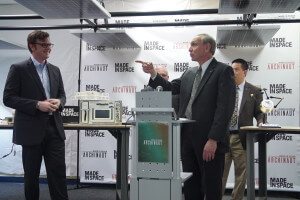
Steve Jurcyk, associate administrator of NASA’s Space Technology Mission Directorate, suggests they’d like to make a 15-meter telescope to image exoplanets. And Rush says Mars is on their mind too.
“Eventually, Archinaut could potentially build and integrate a reflector for telecommunication satellites to beam signals back and forth, or it might add structures to a future human space vehicle, such as a Mars transit vehicle.”
As one of three proposals selected by NASA to advance in-orbit manufacturing, Jurcyk says they hope not only to advance human and robot space exploration, but to also enable new capabilities for US commercial activity in space.
There are still technical challenges ahead. But if successful, it’ll be another important step to a more permanent human presence in space.
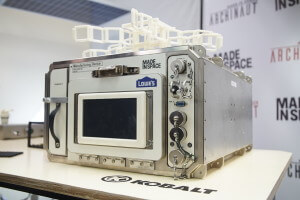
Made In Space has made some incredible strides over the last few years, from getting their 3D printer onto the ISS to printing the first off-planet manufactured tool.
In May, CTO of Made In Space, Jason Dunn, will be discussing the future of space manufacturing at Singularity University’s inaugural Exponential Manufacturing Conference.
Image credit: Made In Space; Jonathan Lee/Singularity University