Visit Singularity Hub for the latest from the frontiers of manufacturing and technology as we bring you coverage of Singularity University’s Exponential Manufacturing Summit.
Take a moment and look at the objects surrounding you.
Maybe you’re reading this article on your computer or cell phone, sitting in a chair, standing at your desk, or riding the local transit system. You may be drinking coffee from your favorite mug or opening the wrapper of your beloved midday snack.
At any moment, there are hundreds, if not thousands, of objects surrounding you that all came from a manufacturing facility. Perhaps more than any other, the force and power of this industry is evident everywhere you look.
Last week at Singularity University’s first-ever Exponential Manufacturing Summit in Boston, we heard from over 50 industry experts across diverse disciplines within manufacturing about the latest technologies and tactics.
In the wake of so much information, common lingering questions include, “How does this all come together?” and “What does it mean?”
We looked at the big picture and distilled the 2016 Exponential Manufacturing Summit into the four big themes we saw emerge during the event.
But as Aristotle said centuries ago, “The whole is greater than the sum of its parts.” All four factors are most potent when they converge. This convergence is shaping the next generation of factories, startups, and technologies in manufacturing.
1. The personal factory is here
Digital technologies have been knocking down barriers to entry in tech and digital media—and now, we’re witnessing a similar effect for the makers of physical stuff. New low-cost, digitally driven manufacturing devices are enabling people to do tasks that were traditionally only possible in expensive facilities and factories.
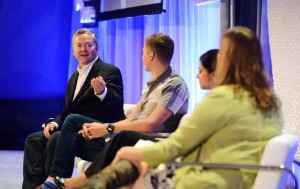
Crowdfunding platforms are fueling the entry of these low-cost machines, like the Makerarm, which raised nearly half a million dollars on Kickstarter, and is the first complete digital fabrication robotic arm that mounts to a desktop.
Combined with a desktop CNC mill like the Othermill, a pair of 3D printers (one for quick prototyping and another for finish work), a laser cutter, and a router—and what you’ve got is an “in-home” factory capable of building factory-quality products.
Danielle Applestone, CEO of Other Machine Co. said during her talk:
“It used to be that you had to go to a factory to build high precision metal things in whatever material—this is no longer true. You can do whatever you want yourself without interfacing with the factory. We can also build electronics in our garages. We can use the most cutting-edge chip sets, shipped directly to us through Alibaba or DigiKey right to our house, build products, put our firmware on them and deliver them to customers without ever having to ask permission.”
Further summit reading:
- The Personal Factory Is Here—and It Will Bring a Wild New Era of Invention
- How the National Science Foundation Is Catalyzing the Future of Manufacturing
2. It’s not about human vs. machine, it’s about human + machine
The winning equation for successful factories will be combining advanced AI with new business processes and models.
For decades, employees and machines have largely worked independently throughout the production process. Industrial robots were simply too dangerous to be near humans. Now, advances in AI and robotics are opening new possibilities for intelligent and efficient human-machine collaboration on factory floors.
Manufacturing robots are finally becoming more flexible, approachable coworkers who are safer to work with.
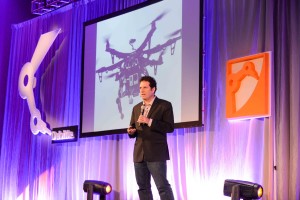
A common example, Rethink Robotics’ Baxter robot, is a factory-ready robot that has eyes to show its human counterparts on the assembly line where it’s looking, and therefore, which task it’s going to do next. Add in the fact Baxter can be programmed just by moving its arms—and you have friendlier, more adaptable bot.
Robotics expert and director of Columbia University’s Creative Machine Labs, Hod Lipson, projected how these advances in AI and robotics will converge to create fully resilient and adaptive cloud-connected factories in the future.
Lipson says, “What one robot knows, it will share with all of the other robots. Manufacturing robots doing inspection and working in factories will gain the experience of a thousand lifetimes, and this accelerated learning will compound all the previous trends.”
Further summit reading:
3. Product innovation has been turned upside down—but don’t overlook the expertise of the big guys
Not only is access to new technologies allowing tinkerers and inventors to turn their garage into a factory, startups in manufacturing have triggered a revolution in how products are created—and massively accelerated the timeline from idea to market.
When you combine these two forces, startups are flipping traditional manufacturing principles on their head. For example, rather than potentially wasting millions of dollars in market research to create “the perfect” product, they’re letting their customers play a key role in the actual product development early on.
Shree Bose took this route with Piper, a computer kit for kids to learn engineering through the game Minecraft and the grand prize winner of Google’s Global Science Fair. Bose said she only built one scrappy prototype of Piper before beginning the Kickstarter campaign. Behind the scenes, she decided that unless the campaign broke their fundraising goal by $100,000, there wasn’t enough demand, and therefore, they weren’t going to move forward with the product.
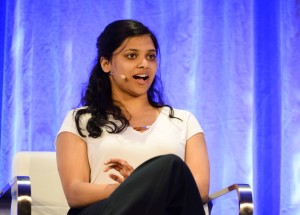
And the biggest players are taking note of this scrappy approach too.
Kevin Nolan, CTO of GE Appliances, demonstrated a successful case study of how a large company can adapt these startup principles to develop new products and showcased the work of FirstBuild, GE’s new product innovation group.
Large companies can reduce risk by letting their community validate an idea first and then staying as lean as possible during product development. Nolan says, “As we try to do this with zero capital investment, lean is our best friend. We don’t make parts until we get orders or we have a purpose for the product.”
Dale Doughtry, the founder and CEO of Maker Media, reminded us that it’s not just about companies taking lessons from startups. Startups can tap into the large body of existing knowledge from mass-manufacturers—especially when it comes to scaling a product for the crowds.
Further summit reading:
4. Organizational agility is an imperative
Peter Diamandis, co-founder and executive chairman of Singularity University and executive chairman of the XPRIZE Foundation, kicked off the summit by citing a study from Yale University, which said:
“If you started a company in the 1920s you had 67 years on the S&P 500 before you were disrupted. Today, if you get on the S&P 500 you’re on it for 15 years.”
Diamandis then hit the audience with three heavy wakeup calls.
- If you thought the rate of change was fast, you haven’t seen anything yet.
- You can either surf on top of this tsunami or get crushed by it.
- The difference between disruptive stress and distributive opportunity is up to you—and this is one reason why you need to care.
Manufacturing giants must welcome this new fast and agile ecosystem or, as Diamandis says, they’ll get “Kodaked.”
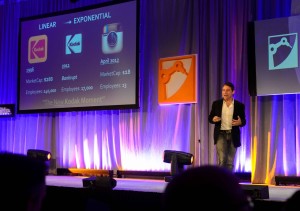
But becoming an agile organization is extremely hard work and counterintuitive to how most companies behave and operate. Further, some parts of the economy are fragmenting such that large companies in those sectors are on shaky ground.
John Hagel, the co-chairman of Deloitte’s Center for the Edge spoke on the decades-long economic trend his group calls the “big shift.” Hagel said the economy is splitting into two parts—products and services are fragmenting into smaller and smaller pieces, while the platforms knitting them together are getting bigger.
This need for organizational agility is one factor that will force large companies to become more innovative in both their operations, management, and strategy.
Speaker Sandy Pentland, director of the Human Dynamics Lab at the MIT Media Lab, showed how big data can help large companies better understand the behavior and communication of their employees and eliminate outdated business practices.
Pentland says, “A lot of the classic arguments we have about why organizations are so bad get broken down by having a little bit of data about how acting like a normal human is actually good for the organization. The bosses, or bean-counters, won’t believe this until you show them data. So, we’re showing them data.”
Further summit reading:
- MIT’s Sandy Pentland: Big Data Can Be a Profoundly Humanizing Force in Industry
- A Big Shift Is Coming, and It Could Uber-ize Entire Industries
Image credit: Shutterstock and Singularity University