This Startup Is Producing the World’s First Carbon-Negative Concrete
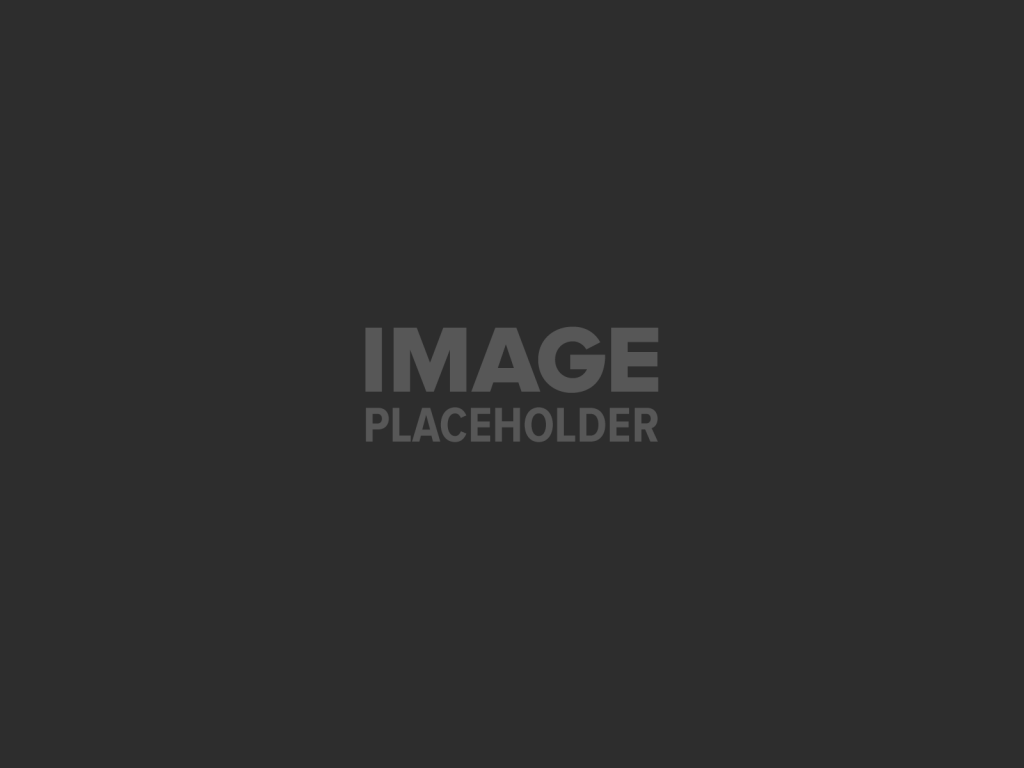
As the sense of urgency around climate change intensifies, most of the focus is on shifting energy production away from fossil fuels and electrifying transport, from cars to buses to planes. Transportation and electricity production are the top two culprits when it comes to emitting CO2 (but also two of the most necessary tools for our day-to-day lives). Third on the list and an equally complex beast is industry, and a big part of industry is concrete.
It’s been said that concrete is the most widely-used substance on Earth after water. It’s all around us, but we never really think about it. Modern society is built on it; it’s in our roads, schools, homes, offices, and more; we can’t live without it. Yet we’re going to have to start trying.
The manufacture of cement, concrete’s key ingredient, accounts for a whopping eight percent of the world’s emissions. We’re not going to stop building things; on the contrary, we’re in the midst of a major housing crisis that’s going to require a lot more building of things (and doing so cheaply). So how do we build strong, durable structures without continuing to harm the planet? What could reliably and affordably take the place, going forward, of the concrete that blankets our cities?
A startup called CarbiCrete has been developing one promising solution: carbon-negative concrete.
CarbiCrete was founded by Dr. Mehrdad Mahoutian and Chris Stern, both alumni of Montreal’s McGill University; Mahoutian started developing the company’s tech as a PhD student. Earlier this year the company secured $17.3 million (23.5 million CAD) in Series A funding.
Status-Quo Concrete
The key ingredient in concrete is cement, a complex compound made from calcium, silicon, aluminum, iron, and other ingredients These are heated to extremely high temperatures (2,700 degrees Fahrenheit!), causing a chemical reaction where some elements burn off and the remaining ones end up as a powder. There’s a double-whammy of emissions from this process: first, coal or natural gas are burned to create the energy and heat needed to reach such high temperatures; and second, the chemical reaction of the cement compounds emits CO2.
The cement powder gets mixed with aggregate materials like sand and gravel, and when water is added another chemical reaction takes places that causes the whole mixture to harden, reaching its full strength in a little under a month.
Earth-Friendly Concrete
CarbiCrete is doing things differently in a couple ways. For starters, they’ve cut out cement altogether and replaced it with steel slag. Slag is the waste that comes from the metal-making process; once iron is extracted from iron ore to make steel, slag is what’s left over. It’s not uncommon to use slag as an aggregate in construction, most often for paving roads.
They mix the slag with aggregate and water, then pour the mixture into forms to make CMUs (concrete masonry units, the concrete blocks used for construction). The last step is to cure the blocks so that they harden and reach full strength. This happens in an absorption chamber into which CO2 is injected, causing yet another chemical reaction; the company’s website explains, “During the carbonation process, the CO2 is permanently captured and converted into stable calcium carbonates, filling the voids of the matrix to form a dense structure and giving the concrete its strength.” Full strength is reached in 24 hours.
Be Part of the Future
Sign up to receive top stories about groundbreaking technologies and visionary thinkers from SingularityHub.


What makes CarbiCrete carbon-negative instead of carbon-neutral is that the company uses CO2 gas sourced from industrial vents in its absorption chambers. So they’re not creating CO2 up front, and they’re sequestering some that’s been removed from the atmosphere.
The company says its CMUs have mechanical and durability properties equivalent to or better than cement-based CMUs, including higher compressive strength by up to 30 percent, and better freeze/thaw resistance.
Scaling Up
One potential drawback, though, is that since the CO2 absorption is a critical part of the process and must be done in a special chamber, CarbiCrete can only be used in pre-cast form; it can’t be put in a mixer truck and poured on-site at a construction location. Rather than selling CMUs, CarbiCrete licenses out its technology to concrete manufacturers, who can implement the company’s technology in precast facilities. Depending on the size of the absorption chamber, the tech could be used to make blocks, panels, beams, or really any other pre-cast product.
CarbiCrete claims that if a typical CMU-producing plant adopts its technology, the environmental impact can be significant, with 20,000 tons of CO2 abated and removed, 4,400 cubic meters of water saved, and 33,000 tons in landfill avoidance annually.
There’s no doubt CarbiCrete’s product seems like the way to go. But in addition to having to be pre-cast, it could be difficult to scale the product’s final curing process to reach the volume necessary to make a dent in traditional concrete use.
Hopefully the company has more innovations up its sleeve that can address its current limitations. Investors seem to think so; last month CarbiCrete secured a new $5 million (USD) from BDC Capital’s newly-launched Climate Tech Fund II, which the founders say they’ll use for working capital, product development, and building out business development and marketing operations.
We're still a ways away from converting to truly sustainable building technology, but carbon-negative concrete, even on a small scale, is a step in the right direction.
Image Credit: Dan Meyers on Unsplash
Vanessa has been writing about science and technology for eight years and was senior editor at Singularity Hub. She's interested in biotechnology and genetic engineering, the nitty-gritty of the renewable energy transition, the roles technology and science play in geopolitics and international development, and countless other topics.
What we’re reading